What began as an experiment in a nine-ounce cup of water has been developed into a full-scale technology that recently became a finalist for a 2019 R&D 100 Award in the mechanical/materials category. Achieving that honor was E-MOP™ — electromagnetic oil spill remediation technology — developed from patents owned by Fermilab. E-MOP uses materials that are environmentally safe, reusable and natural.
“The technology uses electromagnetic pulses and specially timed magnetic fields to produce magnetic forces that move, lift and transport oil,” said Aaron Sauers, Fermilab’s patent and licensing executive. “This provides for an effective and nontoxic method for remediating oil spills both on water and land.”
The U.S. Department of Energy estimates that 1.3 million gallons of oil spill into national waters from vessels and pipelines in a typical year. These spills pose a potentially devastating threat to coastlines, waterways and oceans.
Fermilab licensed the patents used to develop E-MOP technology in 2015 to Natural Science LLC, which was founded by its inventor, Arden Warner, a Fermilab accelerator physicist. E-MOP could also be used industrially to filter and remove clumping substances used in treatment plants and to process and reclaim water associated with fracking and the oil refinery process.
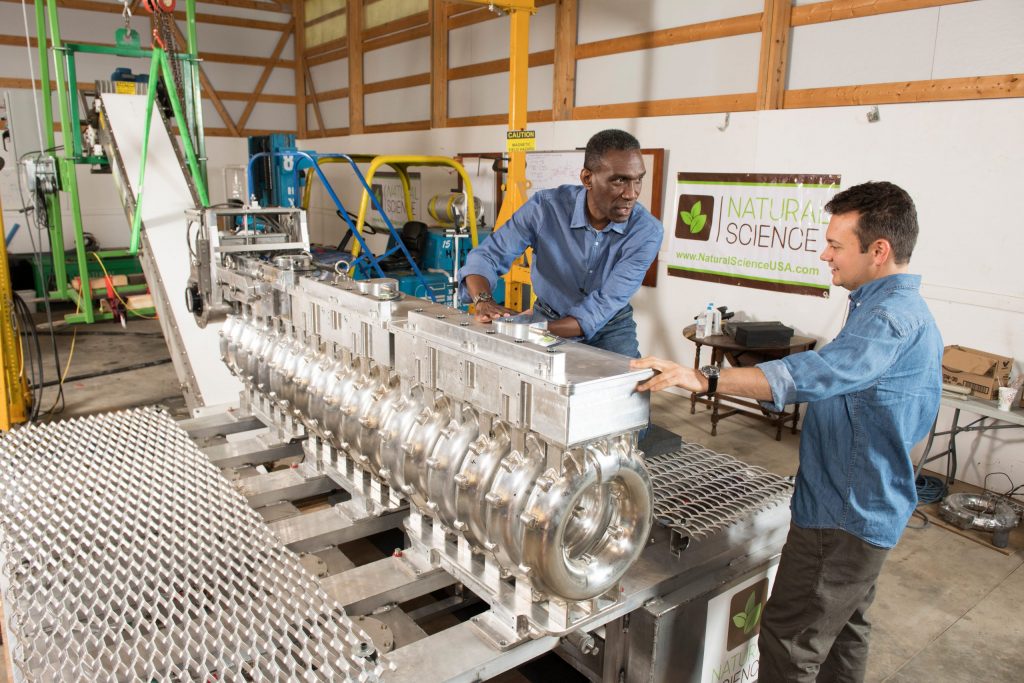
Scientist Arden Warner, left, shows Aaron Sauers, Fermilab licensing and patent executive, the E-MOP system. It consists of solenoidal (doughnut shaped) magnets that are coupled together in groups of six to form a module. Several modules are connected together to form an electromagnetic-boom (e-boom) structure. The system can be made longer or shorter by adding or removing modules to accommodate the situation. Every magnet in the structure is separated from the next by a fixed distance that optimizes the “gradient” effect of the magnetic fields between them. Photo: Reidar Hahn, Fermilab
The technology was sparked by a question that Warner’s wife asked him after the 2010 Deepwater Horizon oil spill in the Gulf of Mexico: “Could we remove oil from water?” It occurred to Warner that electromagnetic forces would probably work.
“Electromagnetic forces always pop into my mind whenever there’s a problem to solve,” he said.
These forces hold electrons in their orbits around atomic nuclei. The electrons interact to form bonds between the elements and molecules that pervade everyday life, from the fires we burn to the chairs we sit on. But engineers can employ these forces in countless devices, including motors, computer hard drives, medical imaging machines and particle accelerators.
The 2010 Gulf oil spill was of special concern to Warner, who grew up in the relatively nearby Caribbean island nation of Barbados. After successfully testing his concept in the water cup, he built a small-scale prototype to evaluate its performance in a large pool.
During the first week of October, his company tested its large-scale prototype in a huge tank at Ohmsett, the National Oil Spill Response Research and Renewable Energy Test Facility in New Jersey. The tank measures 600 feet long, 200 feet wide and holds 2.2 million gallons of ocean water. The tests demonstrated that the E-MOP system was 97.2% efficient in separating oil from water.
“We are getting the oil efficiently off the water without picking up water,” Warner said. “That was our goal, to get it as efficient as we could.”
Spilled oil is first seeded with a small amount of magnetite (less than 0.5% by volume). The system exploits a unique bond that oil forms with magnetite particles at the molecular scale. Magnetite is a naturally occurring magnetic mineral that can be found on most beaches. Heavier than water, the particles sink in the absence of oil. But the presence of oil in water, either on the surface or below, will attract and confine the particles.
“This bond is exploited as the combination of oil and magnetite are rendered magnetic in the presence of magnetic fields,” Warner said. “Viscosity effects are enhanced, the ability to confine, attract and move the spills is increased, and the remediation process is controlled without the use of dispersants and other harmful chemicals and methods.”
Solenoids — coiled wires that produce magnetic fields, together with other magnets — provide the force needed to move the magnetized mixture, collect it and separate the particles for potential reuse and the oil for possible reclamation.
The solenoids form an active electromagnetic boom that fundamentally differs from the passive booms commonly used today. The magnetic boom collects and transports the magnetized mixture within reach of its fields on and below the surface and delivers it to a magnetic ramp.
“This includes mixtures that may be several inches below the surface, as in the case with heavy-oil spills,” Warner said.
R&D Magazine presents the R&D 100 awards annually in recognition of exceptional new products or processes that were developed during the previous year. An international panel of judges selects the awardees based on the technical significance, uniqueness and usefulness of projects and technology from across industry, government and academia.