Engineers at the U.S. Department of Energy’s Fermi National Accelerator Laboratory have partnered with RadiaBeam Technologies, a California-based small business that specializes in accelerator development and fabrication. Fermilab engineers used their expertise in cryomodule design and conduction cooling to help the company break into the superconducting industrial accelerator market. The engineers, part of the Illinois Accelerator Research Center known as IARC, worked with RadiaBeam to design and assemble a conduction-cooled cryomodule.
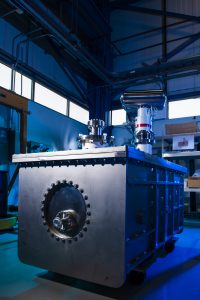
The nearly assembled cryomodule sits in Fermilab’s Heavy Assembling Building at IARC. Photo: Daniel Svoboda, Fermilab.
This partnership, part of Department of Energy’s Small Business Innovation Research program, began in February 2021. The SBIR program encourages U.S. small businesses to engage in federal research and development efforts with the potential for future commercialization of technologies. The cryomodule is fully assembled and on its way to California. There, RadiaBeam will put it through additional testing.
“One of IARCS’s missions is to engage with industry and help transfer technology developed at the lab to our industrial partners,” said Chris Edwards, engineering project manager at Fermilab. “At the moment, industry needs the capability to deliver high enough power and run an accelerator efficiently enough to make a good business case for the use of an accelerator.”
Industry uses accelerators for a variety of applications such as medical device sterilization, isotope generation and more. There are several new markets emerging in the areas of waste remediation, pavement treatment and treatment of PFAS chemicals. Typical industrial accelerators today use room-temperature copper, which is relatively inefficient and expensive at higher power.
In contrast, superconducting radiofrequency accelerators can run at very high power and are much more efficient. However, traditional SRF accelerators often rely on liquid helium to cool their cavities. This introduces a lot of complexity in the infrastructure, as the use of liquid helium requires a cryogen plant, sophisticated machinery and specialized operators. Large companies and scientific facilities like Fermilab have the infrastructure and expertise required to do this; smaller businesses and universities do not.
Fortunately, advances in the cryocooling industry have simplified the cooling infrastructure needed in SRF machines.
“Modern cryocoolers, the units which remove the heat produced in the accelerator cavity, enable conduction cooling of these cavities. This provides a higher cooling capacity at higher temperatures than conventional cryomodules require,” said Charles Thangaraj, technology development and commercialization manager at Fermilab.
RadiaBeam engineers designed the cryomodule with help from their Fermilab counterparts. Their goal was to have a cryomodule with minimum thermal losses. It needed to take full advantage of multistage cryocoolers to conductively cool an SRF cavity to operate within a facility or to be used in the field. The cryomodule included thermal and magnetic shielding and was scaled to fit up to a four-and-a-half cell 650MHz cavity, about the size of a kitchen refrigerator. All purchased equipment and components were procured, fabricated and validated at RadiaBeam before being shipped to Fermilab for assembly and testing.
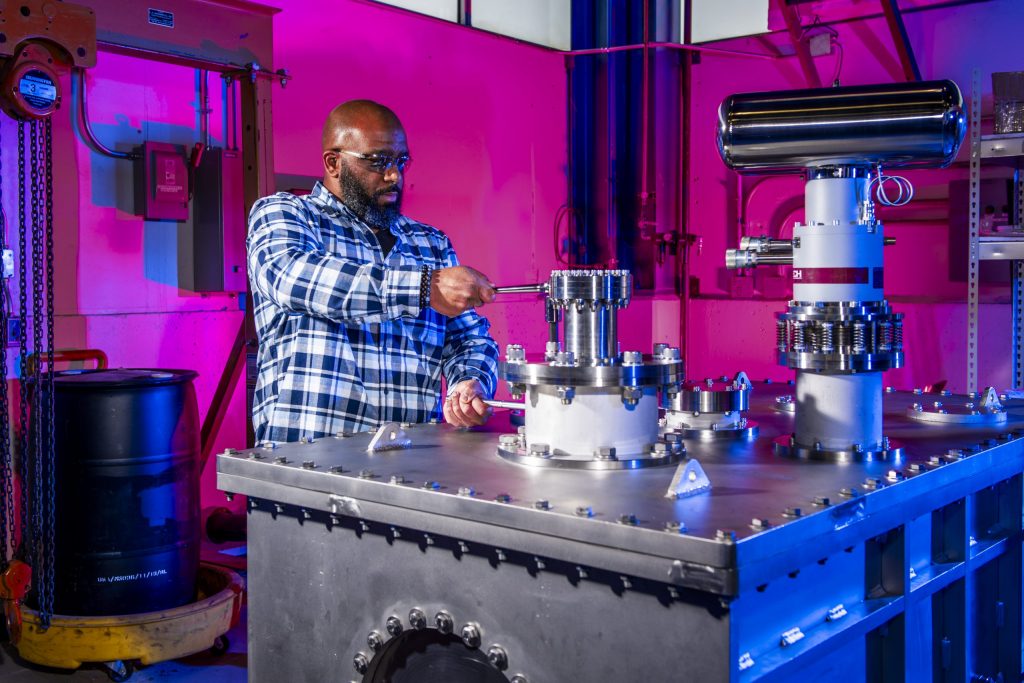
Engineering associate Michael Henry helped assemble a cryomodule that will be used by Fermilab industrial partner RadiaBeam Technologies. Photo: Daniel Svoboda, Fermilab.
Michael Henry, an engineering associate at Fermilab, performed most of the assembly of the cryomodule, which consists of a cryocooler on top and a vessel and cavity inside. He had to build the cryomodule in stages, ordering new components, adding them, and then testing the components as needed. Throughout this process, he regularly worked with RadiaBeam engineers. He kept them abreast of progress, explained any issues and shared solutions or potential solutions they would work together to address.
Once the assembly was complete, Henry and his team tested the vacuum and cooldown systems. After determining the cryomodule was in tip-top shape, they shipped it to RadiaBeam.
“This partnership completely changes the game. Now, we can construct conduction cooled cryomodules that can handle higher-energy electron beams and have an industrial capability to build such modules,” said Thangaraj.
Fermi National Accelerator Laboratory is supported by the Office of Science of the U.S. Department of Energy. The Office of Science is the single largest supporter of basic research in the physical sciences in the United States and is working to address some of the most pressing challenges of our time. For more information, please visit science.energy.gov.