Technical staff at the U.S. Department of Energy’s Fermi National Accelerator Laboratory have completed a prototype of a special superconducting cryomodule, the first of its kind in the world. The national lab is home of the Proton Improvement Plan II, or PIP-II, a project to upgrade Fermilab’s particle accelerator complex.
The new high-beta 650-megahertz, or HB650, cryomodule is the longest and largest cryomodule in PIP-II. It will be responsible for accelerating protons to more than 80% of the speed of light. Ultimately, four of them will comprise the last section of the new linear accelerator, or linac, that will drive Fermilab’s accelerator complex.
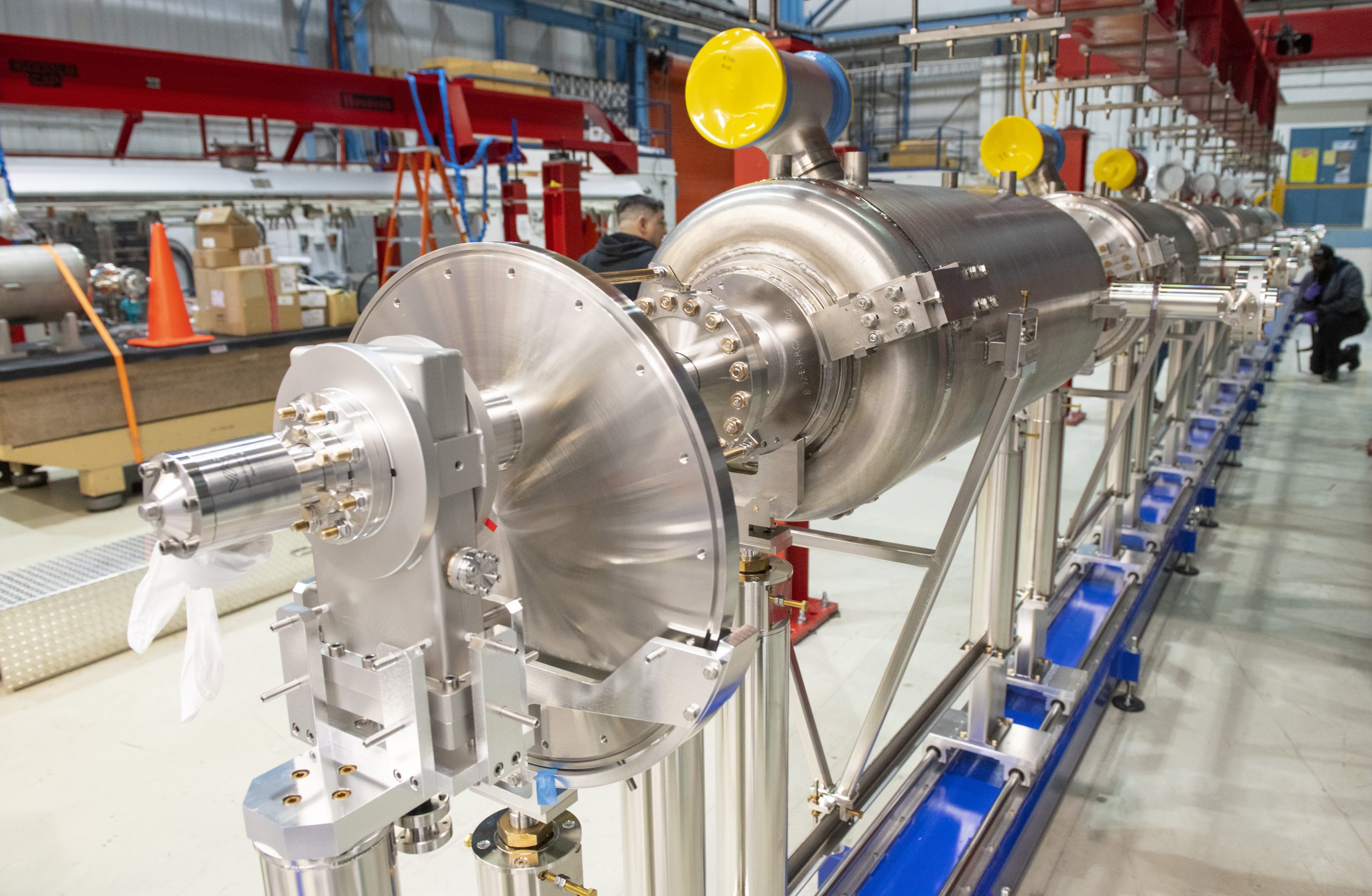
The cavity string for the HB650 cryomodule after being assembled in April 2022. These cavities comprise the heart of the new cryomodule. Photo: Lynn Johnson, Fermilab
In this final section of the linac, these superconducting cryomodules will power beams of protons to the final energy of 800 million electronvolts, or MeV, before the protons exit the linac. From there, the proton beam will transfer to the upgraded Booster and Main Injector accelerators, where it will gain more energy before being turned into a beam of neutrinos. These neutrinos will then be sent on a 1,300-kilometer journey through Earth to the Deep Underground Neutrino Experiment and the Long Baseline Neutrino Facility in Lead, South Dakota.
With the newly completed assembly, the PIP-II team concludes a long process that began in earnest in 2018 with the development of the cryomodule’s design, led by Fermilab. The lab’s earlier development of the lower-frequency SSR1 cryomodule heavily influenced this design. Completed just before work began on the HB650 cryomodule, the SSR1 cryomodules will make up a different part of the new linac.
The HB650’s final design review occurred in 2020; procurement for many of its components began shortly afterward. Assembly started in January 2022 in a new cryomodule assembly facility at Fermilab. Upon its completion last month, the prototype moved from its assembly location to a testing complex on Fermilab’s campus. There, it will undergo a series of checks to validate its design and functionality.
Saravan Chandrasekaran, PIP-II manager for the HB650 cryomodule, said that the team overcame challenges, including a COVID quarantine for the assembly team and supply chain delays.
“I think patience was one of the most important things in this whole process,” said Chandrasekaran. “It took longer and had more complexities to it than we were expecting. But that’s always the case with the prototypes.”
The HB650 cryomodule is a 10-meter-long cylinder, weighing approximately 27,500 pounds. At its core is a chain of “cavities” — what looks like oversized soda cans stacked end to end — made of niobium, a superconducting material. During operation, the niobium must be kept at a frosty 2 Kelvin; at these extremely low temperatures, the niobium loses electrical resistance, allowing beams of protons to accelerate down the linac very efficiently.
To accomplish this close-to-absolute-zero temperature, the team submerges the cavities in a bath of liquid helium. Many layers of insulation then protect the cavities from the “warm” room-temperature elements; they include a vacuum jacket; multiple sheets of thin, highly reflective insulating material, known as mylar multi-layer insulation; an aluminum thermal shield and another coat of mylar multi-layer insulation. Finally, a carbon steel vacuum vessel encapsulates all of these layers. It also acts as one of the cryomodule’s three layers of magnetic shielding to protect the niobium cavities from Earth’s magnetic field, which would otherwise degrade their efficiency.
“We are eagerly anticipating transitioning to the validation phase for this cryomodule, and then on to production of the remainder of the modules.” – Rich Stanek, PIP-II interim project director
The linac will accelerate protons by applying an electrical field in the cavities at radio frequencies of 650 MHz, hence the name HB650. Assembly of the innermost cavity string required extremely clean conditions because any contaminant in the cavity would also be accelerated when the linac is operational, which can cause an electrical breakdown leading to unwanted X-rays or thermal instability. There is no way to clean the cavity once it’s assembled. So, before assembly, the technical team cleaned the cavities with chemical processes and high-pressure deionized-water rinses. In addition, the team took pains to ensure that the assembly area — a newly built cleanroom — was immaculate.
“Just having the clean area is insufficient,” said Chandrasekaran. “In addition to a clean area, the processes and the components that are used within the cleanroom are developed always keeping in mind how to obtain a particle-free string assembly. Even the speed at which team members walk inside the cleanroom is slow because any sudden movement generates particles.”
Over the next several months, the PIP-II team will find out whether all the preparations and precautions paid off. Shortly after the completion of its assembly, the cryomodule was moved to a PIP-II test stand in another building on the Fermilab campus. The team has since installed it and connected it to the cryogenics system. The prototype will now undergo testing at the PIP-II test stand in Fermilab’s Cryomodule Testing Facility, including energizing the cavities. The testing will reveal how well the design and components function.
The PIP-II cryogenic experts just began the process of cooling down the prototype to 2 kelvins to test its resilience to the cold temperatures required for the superconductivity.

The fully assembled prototype high-beta 650-megahertz cryomodule. Four of these will make up the final stage in Fermilab’s new linear accelerator. Photo: Saravan Chandrasekaran, Fermilab
“It’s a prototype for a reason,” said Chandrasekaran. “It’s supposed to be highlighting the challenges, the things that don’t fit together, or things that don’t work as designed before we move on with the production phase.”
Following cool-down, the team will perform a transportation test in which they ship the prototype cryomodule to PIP-II partners in the United Kingdom. It will work similarly to a previous test of a dummy load that occurred last year. Once the prototype has returned to Fermilab, the PIP-II team will test it one more time to ensure all components continue to function.
Once the HB650 cryomodule has been validated, the “real” cryomodules will be built by PIP-II’s partners around the world. Three will come together at Daresbury Laboratory, run by the Science and Technology Facilities Council of United Kingdom Research and Innovation, or STFC UKRI. The fourth will be assembled at Fermilab, using components provided by Raja Rammana Centre for Advanced Technology of India’s Department of Atomic Energy. Ten low-beta 650-MHz cryomodules — similar, but smaller, cryomodules that make up the penultimate stage in the linac — will later be built by collaborators at the French Alternative Energies and Atomic Energy Commission, or CEA.
“We are eagerly anticipating transitioning to the validation phase for this cryomodule, and then on to production of the remainder of the modules,” said Rich Stanek, interim project director for PIP-II.
Chandrasekaran is also excited for the next phase of the HB650 cryomodules. “Each of these challenges that we faced during assembly had their own uniqueness to them,” he said. “Not always could we rely on past experiences to guide us. And, so, navigating them required patience and the expertise that we have in the team and the guidance that we received from several people within Fermilab — and externally as well. That’s the nice thing about this collaboration.”
Fermi National Accelerator Laboratory is supported by the Office of Science of the U.S. Department of Energy. The Office of Science is the single largest supporter of basic research in the physical sciences in the United States and is working to address some of the most pressing challenges of our time. For more information, please visit science.energy.gov.